Inventory management 101: All you need to know
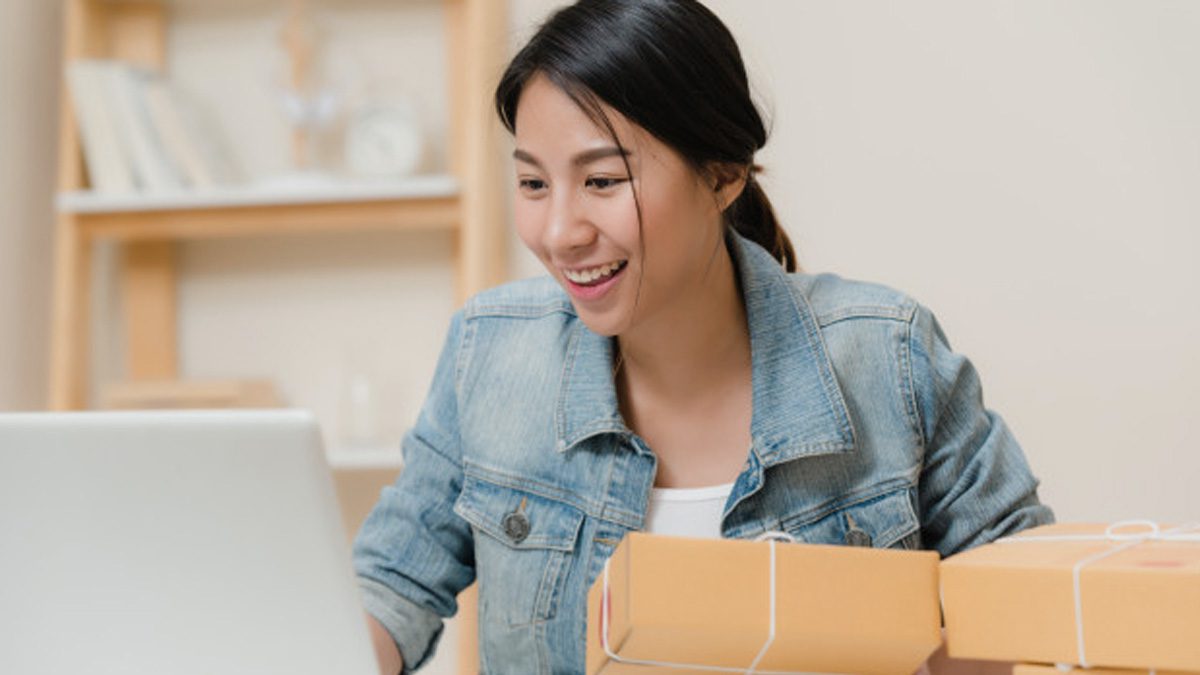
Inventory Management 101: All You Need to Know
Any business or organization has a myriad of functions that are often interrelated and share codependency. Yet, functions like supply chain management, logistics and inventory are considered as the backbone of any business. These functions are quite critical and have the potential to make or break the business. In this article, we are going to discuss the concept of inventory management.
To start with, what is an inventory? Inventory can be defined as an idle stock of physical goods that translate to economic value, and are held in various forms by a business in its custody awaiting packaging, storage, and delivery in a future point of time. Inventory and its optimal management are of utmost importance for the organizations that are into production, trading, sale, and service of various products. Simply put, inventory is a necessary evil for such businesses.
Now, let’s discuss the inventory management meaning. Inventory management can be defined as the system used to organize and track all the physical goods under the custody of the business at any point in time. It is a crucial business function that determines the current state of the supply chain and the anticipated revenue stream, and growth opportunities.
So, what is inventory management system? An inventory management system can enable businesses to ensure appropriate levels of products/stocks are on hand to ensure on-time delivery. Apart from keeping a tab on products on hand, inventory management systems offer data-driven and actionable intelligence pertaining to product stock, delivery, and sales. These insights will help business owners to stay better prepared for ensuring customer satisfaction, and engagement.
The significance of inventory management for business success is undeniable. Here are some of the key functions of inventory management.
- To determine the sufficient amount and type of inventory at various stages
- To facilitate the production and sales process
- To save costs by keeping an accurate level of inventory
Here are some of the cutting-edge inventory management techniques that several businesses leverage to stay competitive.
ABC Analysis:
ABC is the abbreviated form for Always Better Control. Inventories are categorized as A, B, and C as per this inventory management technique. The category A inventories are usually expensive, thus, are closely controlled. The category B inventories are less expensive and thus controlled moderately. The category C inventories have a higher volume, and are least expensive; the control is also minimal for these inventories.
Just-in-Time:
As we have discussed earlier in this article, inventory is the physical goods kept as stock by a business during their entire production, sales, and delivery process. JIT inventory management technique depicts that a particular level of inventory is maintained that is required for the production process.
Businesses may save costs with no excess inventory in hand. Despite its cost-efficiency, this inventory management technique may involve risks. Any delays in replenishing inventory may affect the sales and delivery cycle, and, in turn, affect customer satisfaction.
Economic order quantity
This inventory management technique focuses on taking the decision of how much inventory should be ordered at a given point of time and when the order should be placed. This enables businesses to save costs pertaining to orders, and carrying inventory and ensures that the right quantity of inventory is ordered at the right times.
Material requirements planning
In this inventory management technique, manufacturers usually order the inventory as per the sales forecast. MRP systems collate data from multiple business areas and offer actionable insights on ordering appropriate levels of inventory.
Inventory management is an essential yet critical part of every business. With an effective inventory management system in place, businesses can significantly reduce their various costs like warehousing cost, inventory carrying cost, ordering cost, cost of obsolescence, etc. It plays a crucial role in managing the supply chain of the business and ensuring on-time inventory replenishment.
No comments